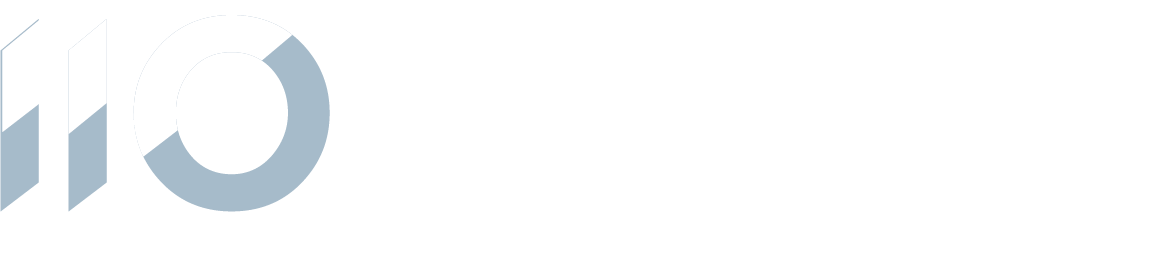
News
Experienced team the key to remediating flammable cladding
The discovery of Aluminium Composite Panels (ACP), also known in the building industry as aluminium cladding, creates a conundrum for building owners.
ACP hit the headlines following the fall-out from the 2017 Grenfell Tower fire in London.
The investigation into the fire that killed 70 people shone a light on the popular but potentially deadly aluminium cladding products used extensively on buildings around the world, including here in Australia.
In NSW, hundreds of buildings are clad in ACP, and many do not meet the building code.
For building owners, it is a complex and potentially costly problem that can require the replacement of an entire building’s exterior.
There is a temptation to go for the quick fix or the cheaper project option.
But the first step should be to call in an expert team like Paynter Dixon.
Paynter Dixon has the experience to turn a major headache into a problem solved.
Paynter Dixon assists clients to navigate the complex process of identifying and managing flammable ACP.
Working up front with the building owner/manager, known in the industry as Early Client Involvement, (ECI) can make a big difference.
Preliminary investigation can often be confined to whether the aluminium cladding is flammable or not.
This limited investigation is quite a restricted view and does not provide enough information to ensure the remedial work is done on time and budget.
Putting together a comprehensive investigation report pays dividends in the long run.
In the case of aluminium cladding, how it is fixed to a building can vary.
For example, the first levels maybe attached using a cassette system on a frame, and then the next level will change to a double-sided tape system.
The project team may have to stop a project and complete an expensive redesign if this is not known initially.
Early Client Involvement can ensure these issues are avoided.
Paynter Dixon takes a disciplined approach to manage flammable cladding projects.
This involves a four-step process:
- Investigation Report
- Project Design
- Authority Approvals
- Construction
This streamlines the whole process.
The project team knows exactly what they are dealing with, and there is no room left for error.
Sometimes, it is not just the complexity involved in fixing the cladding but finding what is underneath.
Cladding can hide a multitude of building sins.
The project can get held-up multiple times if the project team finds sub-structure issues.
And delays mean time and money, with expensive equipment standing idle.
It is not widely understood how the recladding process works.
It is not as simple as taking a panel off and putting a new one on.
Doing the upfront investigation takes more time, but there is a significant cost-benefit compared to delays during the project.
Obtaining the correct reports and approvals is a critical step in the process and often overlooked.
Under legislation introduced in October 2018, to complete ACM replacement works clients are required to get an authority approval.
This can be done by submitting a Development Application, Complying Development Consent or a Fire Order.
Paynter Dixon has a lot of experience in this area.
In fact, Paynter Dixon was the first company to get approval from the City of Sydney for ACM replacement work under the new legislation.
Paynter Dixon has experience working on multi-storey projects to small single story cladding replacement.
When it comes to cladding replacement, experience counts.
Categories
Related Articles
-
CODA tower crane dismantled
December 02, 2024
-
110 Year Anniversary: narrated history
November 14, 2024
-
110 Year Anniversary: future roads of innovation
October 21, 2024
-
110 Year Anniversary: James and Garry Boyd reflect on success
June 06, 2024
-
Empowering people and projects with standards
May 31, 2024